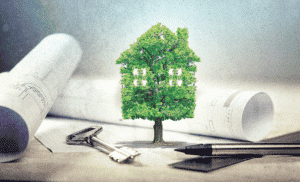
Plant-based insulation methods are popular with consumers due to the high proportion of recycled material used in their production.
To many Americans, home insulation conjures up images of pre-cut rolls of fiberglass “batts” tucked between the inner studs of walls, floors, attics and ceilings.
Today, fiberglass insulation remains one of the most popular forms of home insulation in the U.S., according to industry data, and it’s expected to reign at the top for some time.
But the seemingly hidebound world of insulation is changing, as new products are introduced, old products are updated and consumers demand ever more efficient, affordable and environmentally friendly insulation products.
As a result, the insulation industry, and its related offshoots, today abounds in a dizzying array of new and updated terminology that the average homeowner may struggle to understand.
“There’s been a lot of changes over the years,” Rob Calnan of Waltham-based Calnan’s Energy Systems Inc, said of all the new insulation products and installation techniques on the market today.
New State Pilot Program
In the insulation world, it ultimately all comes down to three things: the estimated “R value,” or the all-important energy efficiency measurement of insulation products; the cost of products and services; and the eco-friendliness of products and services, as exemplified by the “embodied carbon movement,” which tracks the amount of carbon that’s used to produce various energy-efficiency products.
“Insulation improvements and innovations are happening all the time,” said Aaron Gunderson, director of Passive House of Massachusetts, a non-profit that promotes energy-efficient new homes.
If the commonwealth of Massachusetts has its way, the use of new and updated insulation products and installation techniques may well accelerate in coming years, depending on the findings of the ongoing pilot “Market Value Performance” (MVP) program overseen by the state Department of Energy Resources.
According to Ian Finlayson, deputy director of the energy efficiency division at DOER, the goal of the $3.5 million program is to explore ways to increase energy savings and then possibly weave some of the program’s findings into future conservation/energy efficiency policies. The specific areas being explored are insulation, heating system upgrades and air sealing of buildings.
The strategy: Give participating contractors the flexibility to try new and old ways of improving the energy efficiency of buildings – and keeping close track of exactly what’s being done and the specific energy savings involved.
Cellulose Challenges Fiberglass as Favored Material
Calnan’s Energy Systems is an MVP contractor – and it’s focusing mostly on a tried-and-true method of insulating new and retrofitted homes: Cellulose “blow-in” insulation, which uses ground-up recycled paper, such as newspapers, treated with fire–retardant chemicals. Cellulose products have been around for years – rivaling fiberglass batting in popularity – but their quality has consistently improved over the years, Calnan said.
Chris Alphen, general manager of Dolphin Insulation in Littleton, said he prefers cellulose insulation for a number of reasons: It’s not toxic; it retards fire, mold and mildew; and it “manages humidity well.” Its “R value” is lower than spray-foam insulation, but it’s ecologically friendly and preferred by many property owners because of its high use of recycled materials.
One insulation product making a big comeback, also with modern innovations, is so-called “mineral wool” (also commonly referred to by some as “rock wool”), whose origin as insulation dates back to the 19th century and today is experiencing a resurgence in popularity due to its eco-friendliness. It refers to products made from recycled glass, basalt, rocks and slag from steel mills, all of which are ground up and spun into wool-like insulation materials and products.
If the commonwealth of Massachusetts has its way, the use of new and updated insulation products and installation techniques may well accelerate in coming years.
The “wild west” of insulation, as one insulation contractor called it, is “spray foam insulation” — and it’s considered by far the most energy efficient insulation product in terms of R value. But it’s also at least one-third more expensive than other insulation products.
Robert Whitmyer, owner of Genesis Insulation LLC in Newton, says his firm primarily uses spray-foam products divided into two categories: “closed cell” (or more dense foam), usually used in basements and within framing studs, and “open cell” (which expands more quickly in building cavities), usually used on exterior walls and roofs.
“There are a lot of new products out there,” said Whitmyer of spray foam. “More and more people are requesting it.”
Another emerging option is so-called “rigid insulation” product, or closed-cell foam boards.
Lingering Consumer Concerns
But industry officials say there are lingering concerns among consumers, and some contractors, about health and environmental risks associated with spray-foam products. That, combined with its higher prices, is somewhat limiting its adoption.
And an area of growing interest is related to increasingly sophisticated “dedicated air barrier systems,” or membrane-like materials similar in concept to tar paper that are used to cover air leaks in exterior walls, as well as deal with moisture and humidity problems associated with insulation products.
“The point is to provide a continuum of level of insulation” on the outside walls of structures, said Gunderson of Passive House of Massachusetts.
Rachel White, chief executive of Byggmeister Design and Build in Newton, said she’s encouraged by all the innovations now going on within the home energy efficiency market, including new and improved insulation products.
“In the end, it’s all about savings — energy savings and [financial] savings,” she said.