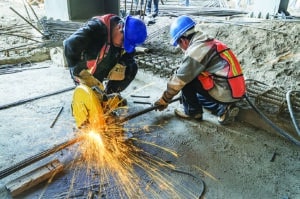
A new report from consultants Turner & Townsend claims Boston is more expensive to build in than London, thanks in part to high labor costs.
Everyone knew Boston was uber expensive to build in. But this expensive?
The Hub is No. 7 on the Turner & Townsend’s top 10 most expensive cities to build in. We are not talking just about the United States or, more broadly North America, but the entire world.
That’s right, Boston right up there with notoriously expensive markets to build – or to pretty much do anything at all in – like Tokyo, Hong Kong, New York and San Francisco.
Heck, Boston is now an even pricier place to build than London (No. 8) and Los Angeles (No. 9).
Needless to say: Hold the champagne, for this is a list no city really wants to be on. Soaring construction costs are one of the ugly side effects of vaulting onto the world stage and becoming a city everyone wants to live or do business in.
In fact, the increases may actually be a “a bit higher than T&T notes,” said James Kirby, president and CEP of Boston-based Commercial Construction Consulting.
“The overall Boston construction market weathered the 2020 COVID storm and the predicted softening of pricing did not occur,” he said.
Yet while the Turner & Townsend report is spot-on about some of the factors behind the big increases, it falls short in one key regard, trying to off-load a big chunk of the blame on the workers building all those new towers taking shape on the skylines from Boston to Abu Dhabi.
Increases Threaten Project Finances
The report is right on target when it points to rising material costs amid the disruption to supply chains around the world caused by COVID-19, which clearly have helped push construction prices up.
Steel prices have surged over the past year in the U.S. and Europe, with the cost of “US hot rolled band,” as the industry calls one benchmark measure, hitting S$1,824 per ton, more than triple its per-ton price a year ago of $572.
Copper prices have also just about doubled over the same period, surging to the $10,000 a ton mark from $5,500 a year ago.
And of course, we all know what’s happened to lumber prices.
“These inflationary pressures are cause for concern, impacting the financial viability of projects,” the T&T report notes.
Beyond the price of copper and steel, you don’t have to do deep textual analysts to see what the T&T report is fingering as one of the big factors driving up costs.
The report gives rising labor costs a starring role as the villain here – maybe not so surprising given the report is written for a corporate audience.
North America, the report notes, has the highest construction wages, with New York and San Francisco leading the way at an average of $109 and $104 respectively, health and various fringe benefits presumably included.
While Boston’s average wage is not listed, it’s likelier than not to be approaching $100 an hour as well given that Chicago’s average hard-hat wage, where the cost of living is significantly lower, is now approaching $75 an hour.
Labor Costs Are a Red Herring
The business community has loved to bellyache about wages since time began.
The development and construction sectors are certainly no exception to that, with a long-standing undercurrent of grumbling among developers about the high cost of union labor in Boston.
And wages, on the surface anyway, would appear to be more fungible than material costs or other factors driven by distant factors, like demand in China or disruptions to distant supply chains.
After all, if wages are too high, can’t you just cut them?
It’s a red herring. If you are doing business in city with long and strong union tradition like Boston, New York, San Francisco or Vancouver – basically the places where everyone in the world wants to be – you’ll have better luck trying to bend the price of steel than in trying to cheap out on the wages you pay.
Wages here and other high-cost-to-build-in-markets are hardly a sign of worker greed, but rather the increasingly insane cost of living in these very same cities.
The Real Cost Centers
The real culprits, if you want to talk labor costs, are cumbersome city and state approval processes and NIMBY opposition, which add copious lawyer’s fees, design changes, interest payments and other carrying costs galore to any project. This one-two punch has killed, delayed and downsized countless projects and led to a dire shortage of new housing over the past few decades, pushing rents and single-family and condominium prices well beyond the means of the average construction worker, even at union wages.
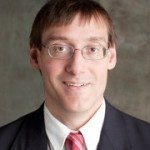
Scott Van Voorhis
And there’s data to back that up, even in the T&T report, skewed as it is towards a comfortably complacent corporate clique.
There’s a big reason average construction wages in Houston, at $57 an hour, and Chicago, at nearly $75 an hour, are lower than in Boston.
It’s the cost of housing, with $299,000 the average price of a home in Chicago, and $217,000 in Houston, according to Zillow. In Boston, by contrast, it’s nearly $700,000.
So, the next time someone tells you it’s the workers’ fault that we can’t build cheaply, show them the local real estate listings.
Scott Van Voorhis is Banker & Tradesman’s columnist; opinions expressed are his own. He may be reached at sbvanvoorhis@hotmail.com.